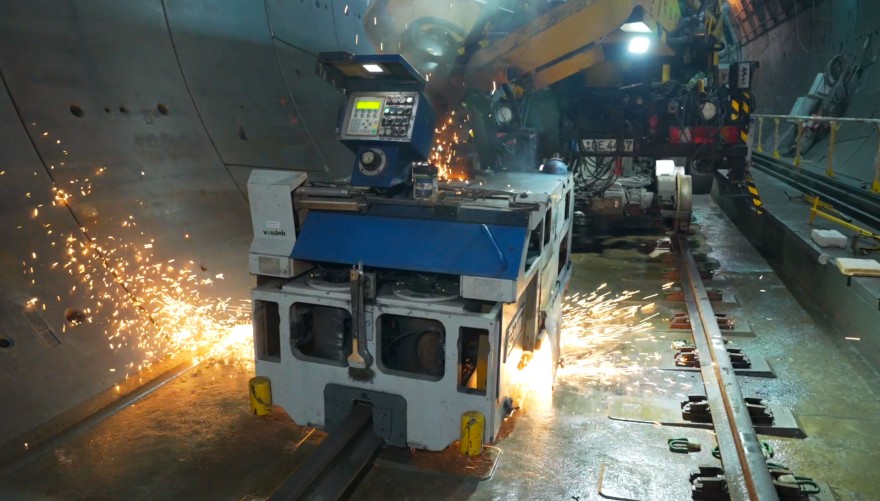
Mobiles RA-Schweißen – vollautomatisches Verfahren für höchste Präzision
Das Abbrennstumpfschweißen ist ein Verfahren, bei dem elektrisch leitfähige Werkstoffe mit großen Querschnitten durch elektrischen Strom bis zum Aufschmelzen erhitzt und mittels Druck zusammengefügt werden. Während des Schweißens besteht immer nur kurzzeitig Kontakt zwischen den Schienenenden. Durch die daraus resultierende hohe Stromdichte wird an diesen Kontaktstellen das Material verflüssigt und verdampft bzw. spritzartig weggeschleudert. Somit werden durch das Abbrennen auch eventuelle Verunreinigungen beseitigt.
Wir favorisieren das mobile RA-Schweißverfahren aufgrund seiner hohen Qualität sowie des schnellen Arbeitsfortschritts. Da die qualitativen Anforderungen und technischen Normen der Regelwerke für das mobile wie stationäre Schweißen – hier zur Herstellung von Langschienen – identisch sind, erhalten Sie mit Vossloh immer die höchste Qualität im Gleis.
Prozessbeschreibung
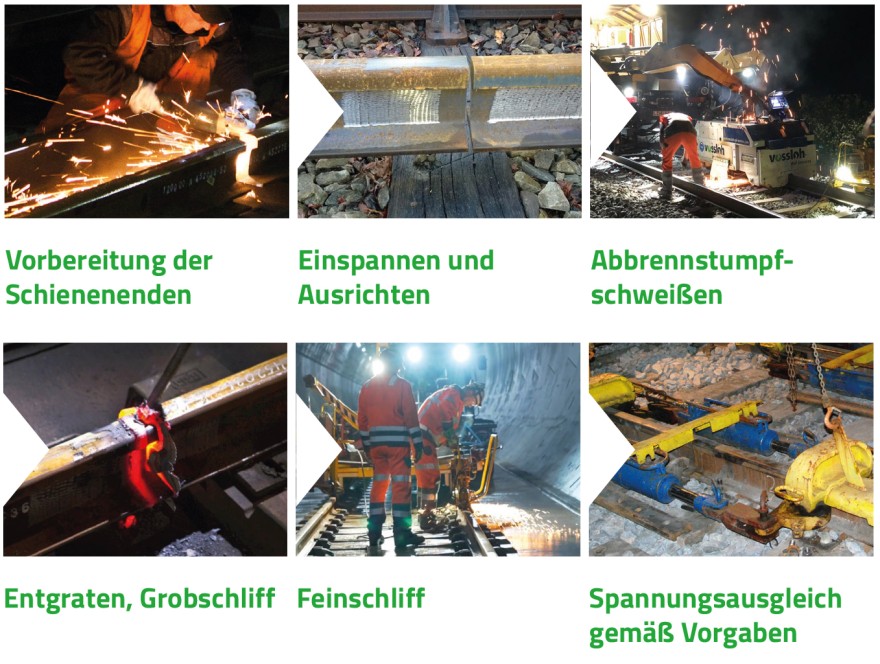
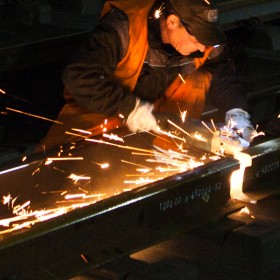
1. Vorbereitende Maßnahmen:
Herstellung sauberer Kontaktflächen für einen Stromeintrag und des Bereiches der zu verschweißenden Schienenenden.
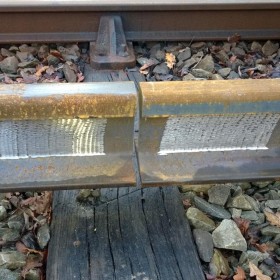
2. Exakte Ausrichtung der Schienenenden zueinander und Spannen für eine sichere Kraftübertragung. Durch explosionsartige Verdampfung an den Kontaktbereichen spritzt ein Teil des Material heraus, in dessen Folge muss zwecks Kontakterhaltung auch während der Aufheizphase eine Vorschubbewegung erfolgen. Dabei unterscheiden wir zwischen der „festen“ Schiene (Standort der Schweißmaschine) sowie einer beweglichen (zu verschweißenden) Schiene. Sind beide Schienen im Schweißkopf ausgerichtet und gespannt, stehen die Schienenenden stumpf zueinander.
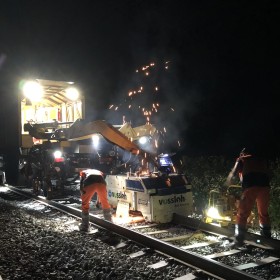
3. Abbrennstumpfschweißen in 3 Phasen
a. Elektrische Spannung liegt an beiden Schienenenden an.
b. Die bewegliche Schiene wird mittels hydraulischer Kraft in sehr kurzen Intervallen zur festen Schiene herangepresst und wieder weggeführt.
c. Durch den entstehenden Lichtbogen erwärmen sich die Schienenenden.
d. Im Moment des Kontaktes entsteht durch Kurzschlussstrom eine große Wärme. Die Schienenenden werden bis auf 1.400°C erhitzt und die Zone des erwärmten Materials wird deutlich erweitert.
e. Beim abschließenden Stauchschlag werden die Schienenenden mit bis zu 600 kN zusammengefügt, Oxide und Verunreinigungen in die Wulst gepresst und festgehalten. Dabei werden die Länge des abgebrannten Materials, die Kraft mit der die Schienen zusammengepresst werden und der Strom, der durch die Schienen fließt, erfasst und in einem Diagramm dargestellt.
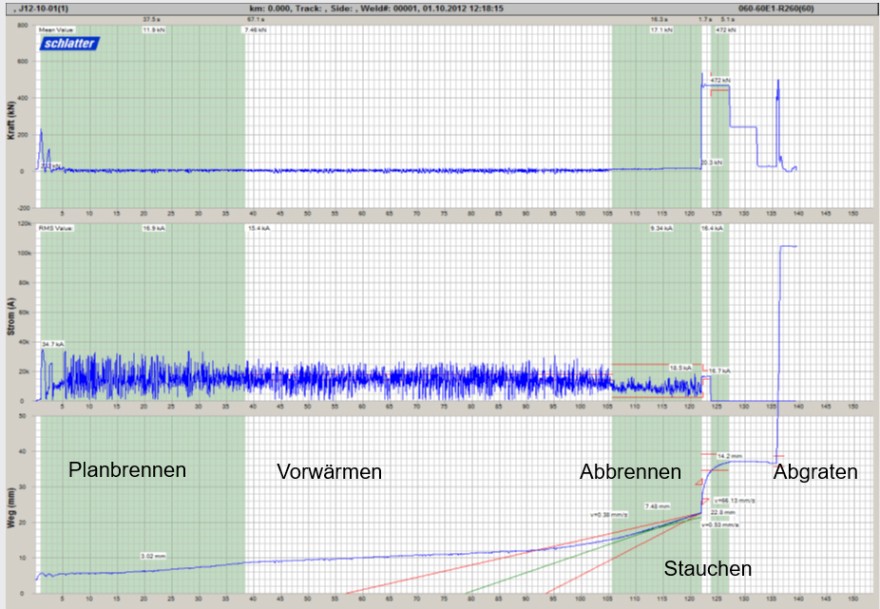

4. Entgraten, Grobschliff
Im noch erhitzten Zustand wird die entstandene Schweißwulst abgeschert und durch Grobschliff eine Profilangleichung hergestellt.
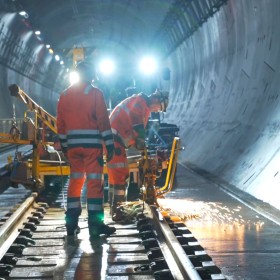
5. Feinschliff
Wenn die Schiene abgekühlt ist, erfolgt der Feinschliff.
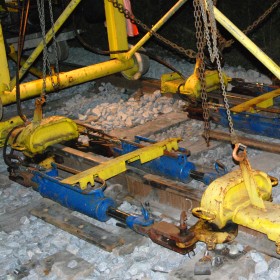
6. Spannungsausgleich gemäß Vorgaben
Die Lücken, die durch Verlegen des Stoßes ins Schwellenfach, das mobile Schweißen und die Herstellung des Spannungsausgleichs am Ende eines jeden Streckenabschnitts entstehen, werden durch Passstücke ausgeglichen.
Einsatzbereiche und -grenzen
- Unsere Teams waren bereits auf drei Kontinenten – ob Vollbahn, Hochgeschwindigkeit, Nahverkehr oder Depot – im Einsatz
- Umgebungstemperatur: -10°C bis 55°C
- Arbeitshöhe: bis 3.000 m über NN
- Kleinster Radius: 350 m
- Steigung/Gefälle: 40 ‰
- Schienenprofile:
Vignolschienen 36 – 68 kg/m (S41–R65) – keine Rillenschienen - Schienenlänge:
- bis 120 m ohne Einschränkungen
- bei Verwendung „weicher“ ZW – Schienen auf Rolle setzen
- Schienen ab 180 m – Schienen auf Rolle setzen
- 180 bis 300 m – Schienen auf große Rollen setzen - Nicht in Weichen und als Schlussschweißung anwendbar
Follobanen-Tunnelprojekt: Mit Hochgeschwindigkeit 100 Meter unter der Erde
Im dritten Quartal dieses Jahres unterstützten wir das Follobanen-Projekt südöstlich der norwegischen Hauptstadt Oslo. Vossloh ist derzeit das einzige Unternehmen, das in Norwegen die Zulassung für das mobile Abbrennstumpfschweißen besitzt. Innerhalb von fünf Wochen führte das Vossloh-Team im fast 20 km langen Tunnel fast 700 Schweißungen mit seinem Schweiß-LKW durch. Abschließend erfolgte der für Hochgeschwindigkeitsstrecken vorgegebene zehntelmillimetergenaue Feinschliff, um die Arbeiten termingerecht abzuschließen.
Großeinsatz auf den Hochgeschwindigkeits-strecken in Deutschland
Während der aktuell stattfindenden Generalüberholung verschiedener Hochgeschwindigkeitsstrecken in Deutschland sind höchste Flexibilität, Teamarbeit und maximale Einsatzbereitschaft gefragt. Bei Projekten dieser Größenordnung besteht die logistische Herausforderung oft darin, dass mehrere Gewerke gleichzeitig in den Bauabschnitten arbeiten. Auf dem ersten Bauabschnitt der SFS 1733 zwischen Hannover und Göttingen kümmerten sich rund 35 Vossloh-Mitarbeiter einschließlich der kaufmännischen Disposition um die Koordination der täglichen Anforderungen. In insgesamt 70 Schichten wurden auf der 90 km langen zweigleisigen Hochgeschwindigkeitsstrecke und in den Tunnelsegmenten über 1.500 Schweißungen durchgeführt. Das Abbrennstumpfschweißen wurde in Kombination mit dem notwendigen Spannungsausgleich, der sogenannten Neutralisation der Schiene, umgesetzt. An Weichen, Bahnübergängen und als Schlussschweißung wurden zudem ca. 140 SKV (Schweißen mit kurzer Vorwärmung)-Schweißungen durchgeführt. Dieses Verfahren ist ein aluminothermisches Gußschmelzverfahren mit kurzer Vorwärmzeit, bei dem durch einen exothermen Prozess das Metall verflüssigt und in den mit Formen umkleideten Schienenstoß geleitet wird. Zum Nachweis der Fehlerfreiheit wurden hier anschließend die notwendigen Ultraschallprüfungen durch das Vossloh-Inspektionsteam ausgeführt. Des Weiteren erfolgte eine Abnahme der Qualität des Schienenlängsprofils an Fahrkante und Fahrfläche, da sich eine optimale Gleisgeometrie auf die Sicherheit und die optimale Lebensdauer der Schiene auswirkt. Bei Geschwindigkeiten größer 230 km/h akzeptiert die DB in einem Bereich von 50 cm vor und hinter der Schweißung auf der Fahrfläche eine Toleranz von höchstens 0,1 mm. Obwohl eine gute Schweißung schon recht glatt ist, lässt sich diese Präzision jedoch nur mit handgeführtem Schleifen durch erfahrene Fachleute erzielen.
Beschleunigter Baufortschritt beim Sneltram-Projekt in Utrecht:
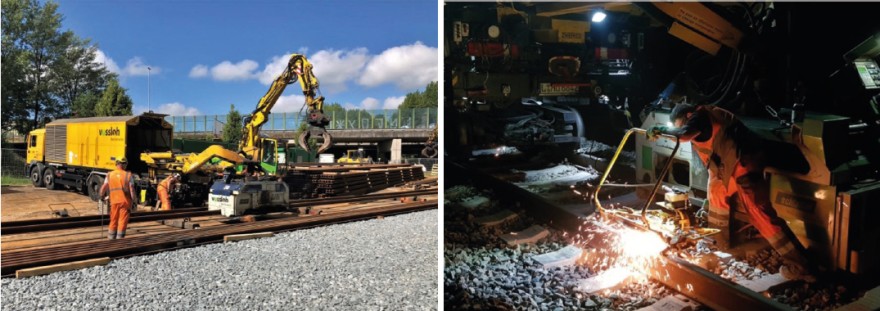
Beim Sneltram-Projekt in Utrecht erzielten wir durch die Vorabproduktion zu Langschienen entsprechend dem Schienenband in Baustellennähe einen beschleunigten Baufortschritt und
1. … minimierten die Schienentransporte
2. … reduzierten die Anzahl der Schweißungen im Gleis
3. … erhöhten die Qualität der Schweißungen dank des RA-Schweißens.
Die 30 m langen Vignolschienen wurden mit Baggern den temporär eingerichteten Schweißstationen zugeführt und nach dem Verschweißen auf 120 m-Langschienen mit Flachwagen direkt zur Baustelle abtransportiert. Insgesamt haben wir über 850 Schweißungen durchgeführt, wobei die Ausführung von fast 60 Schweißungen innerhalb von neun Stunden selbst für uns ein echtes Projekt-Highlight darstellte.
Metro Doha: Arbeiten auf engstem Raum
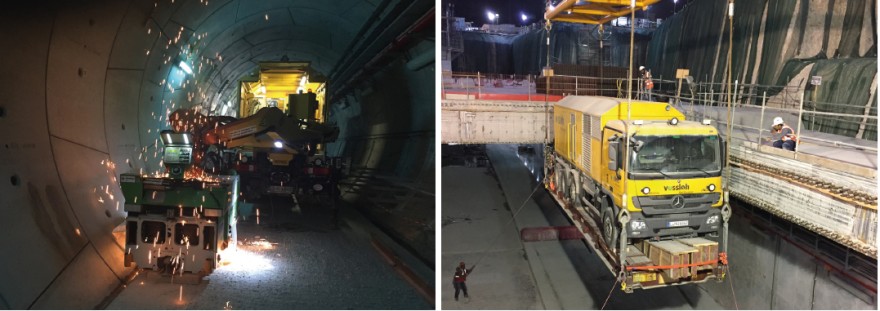
Zu den besonderen Projekten gehört sicherlich der U-Bahn-Neubau in Doha. In Vorbereitung auf die Fußball-WM 2022 in Qatar entstand ein 76 km langes Metronetz mit drei Linien und 37 Stationen, das den Flughafen mit der Innenstadt sowie den Stadien verbindet. Hierfür wurden 18 m lange Schienen per Schiff aus Japan angeliefert, mit einem Kran in den Tunnel eingebracht und ebenfalls in der Art einer semistationären Anlage zu 108 m Langschienen vorproduziert. Anschließend wurden diese dann im Tunnel zum lückenlosen Gleis verschweißt. In 10 Monaten haben wir auf engstem Raum bei Temperaturen von teilweise fast 40 °C und extrem hoher Luftfeuchtigkeit in einigen Monaten – trotz Nachtschichten – etwa 4.000 Schweißungen ausgeführt. Dabei kam uns zugute, dass im Tunnel aufgrund des einheitlichen Temperaturgefüges kein Spannungsausgleich mit hydraulischen Ziehgeräten vor dem Verschweißen notwendig war. Eine exakte Schienenlängung erfolgte lediglich im Bereich 120 m in den und aus dem Tunnel, damit der Schienenstrang bei hohen Temperaturen die Druckkräfte und bei entsprechend niedrigen die Zugkräfte aufnehmen kann. Parallel zu den Hochbauarbeiten an den Wagendepots und Instandhaltungshallen fertigten wir außerdem Langschienen für die Verbindung der zahlreichen Weichen.
Download
Nutzen Sie die Vorteile des professionellen mobilen RA-Schweißens
- Höhere Qualität und Festigkeit
- Prozessstabilität durch Prozessorsteuerung
- Keine Verwendung von Fremdmaterialien (wie Elektrode, Form-Sand, Thermit-Material), deshalb auch keine Einschlüsse, Schlacke oder Schweißrückstände
- Hohe Stückzahlen in kurzer Zeit (bis zu 8 RA-Schweißungen pro Stunde)
Gerne unterstützen wir Sie beider Realisierung Ihres Projektes.