Research and Development
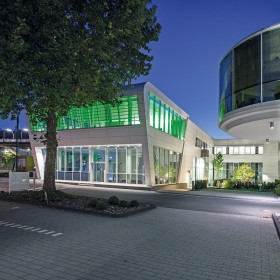
Vossloh is a technological leader in the rail infrastructure segments in which it operates. Innovation plays a decisive role in ensuring that the Company remains competitive from a technological standpoint. In the interest of safety, Vossloh’s products and services are subject to detailed technical specifications and standards that must be met. Before products and services for rail infrastructure are ready for market, they usually undergo (further) development and testing for several years, as well as complex approval procedures by independent testing institutions. Research and development projects at Vossloh are therefore usually scheduled to run for several years.
To satisfy the specific expectations of customers in individual market regions over the long term and reinforce its own competitive position, Vossloh adopts a structured approach to managing innovation by continuously investing in the development and optimization of its products and services. Principles and procedures are defined in the Group-wide Innovation Playbook adopted in 2021, the implementation of which is ensured by a Group Innovation Committee. Vossloh intends to increase collaboration across business units to develop new products, services and business models and ensure that customers and suppliers – with their specific expertise – are involved more closely in research and development processes. After reviewing its production processes over recent years, the company is now implementing a range of measures which will provide ongoing efficiency gains, including modernization, increased automation and specialization.
One focus of innovation at Vossloh is digitalization as the link between hardware and services. The company uses specialized sensor systems to collect data about load levels and track condition and, since 2023, data on the condition of rail vehicles. Among other things, this data can be used to gain knowledge about the degree of wear and damage to track components. With this knowledge, statements can be made about which maintenance strategies should be applied and when. This can reduce the risk of component failure – and thus the unavailability of routes and infrastructure – during ongoing operations. Artificial intelligence also plays an important role in detecting wear patterns to predict the failure of track components and prevent these failures by planning maintenance measures ahead of time. Vossloh uses its in-depth knowledge of rail structure to meet its customers‘ main requirement “increasing track availability” and develop comprehensive solutions in partnership with all business units. Under the guiding principle of “enabling green mobility“, these ensure that the rail infrastructure is more robust and resilient and that route availability is increased, even though the demands on the rail network are constantly increasing.
You can find detailed information on Research & development here.
Core Components
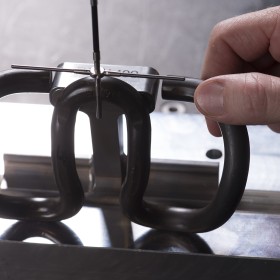
In 2024, the R&D experts in the Fastening Systems business unit of the Core Components division focused, among other things, on further developing the tension clamps of the new M generation. One of the requirements was to increase the service life of the components in heavily used tracks. The potential of rail fastening systems with M clamps in ballasted track was also validated in complex measurement campaigns. Sustainability aspects were at the forefront of the development of new and improved plastic components. The combination of highly elastic rail fastening systems with highly elastic damping intermediate layers has resulted in a new solution for slab tracks. The Tie Technologies business unit again focused its R&D activities in the reporting year on material and energy-saving changes to the composition of concrete for railroad sleepers. The track tests were continued with a product whose cement mixture leads to a significantly improved CO2 balance while maintaining the same properties.
Customized Modules

In the Customized Modules division, the R&D experts focused on life cycle cost analyses, for example, for a complete streetcar network, as well as on the recycling and reuse of turnout elements. Vossloh can now offer manganese crossings that consist of up to around 90 % recycled material. This is linked to changes and adjustments to production processes, which are being geared more towards the circular economy. Several turnout solutions were also further developed in 2024 with a view to reducing CO2 emissions during all phases of the vehicle’s life cycle. The existing methods and models for inspecting and monitoring turnouts on the track have been improved with the help of new software. In general, advancing digitalization was an important R&D topic throughout the division. This is why Building Information Modeling (BIM) is playing an increasingly important role, both in internal processes and in collaboration with customers.
Lifecycle Solutions
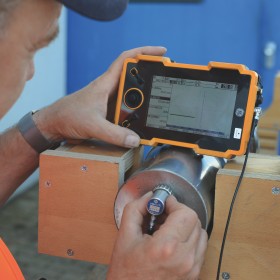
In the Lifecycle Solutions division, (further) development work focuses on machines for rail processing on the one hand, and onboard measuring systems for even more comprehensive condition monitoring of rail lines and software for evaluating and displaying the overall data (keywords “smart maintenance”) on the other. In 2024, the control, sensor and measurement technology of various grinding and milling vehicles was also adapted to further customer requirements. An improved version of the successful high-speed grinding train is in preparation (“HSG-next”). The installation of a measuring system that measures and documents the quality of machined new rails began in the welding plant. The development of the RailTainer for efficient rail transportation to construction sites made further progress, as did the development of a loading and unloading system for transporting the VTM-c local milling machine with a RoMo wagon.