High performance milling doesn’t use water and produces neither sparks nor dust. The metal chips removed are extracted during the milling process and deposited in chip bunkers for later disposal. These bunkers have capacities of several tons, which is sufficient for several work shifts. Not only does this render unnecessary the cleaning of tunnel walls after a milling run, for example, it also makes Vossloh’s VTM-performance the safest and most environmentally-friendly rail milling machine in the world.
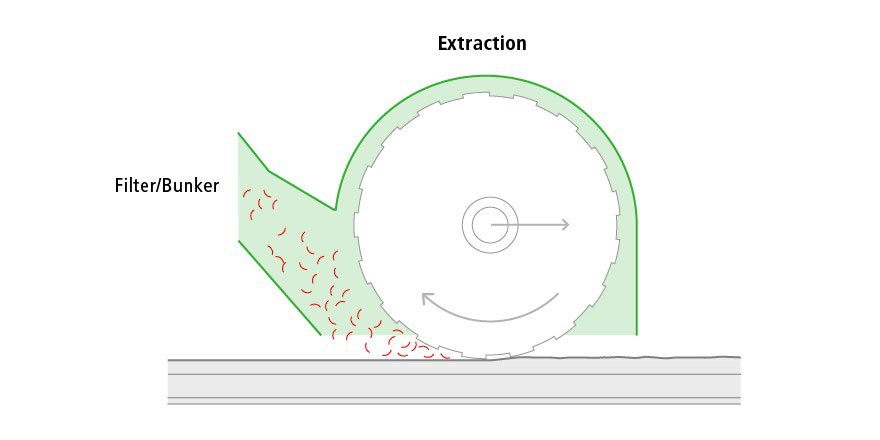