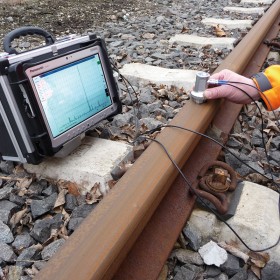
Vossloh employs the most modern testing and measuring technology together with certified, highly specialized personnel who possess extensive knowledge on all the stages of the rail’s life cycle.
There’s a choice of various testing and inspection methods to detect irregularities in the rail, and special software is used to analyze and prepare the results for interpretation.
Experts then use the data collected as the basis for selecting the most economical maintenance procedure and determining its process parameters.
Vossloh uses the following testing and inspection methods:
Visual inspections
A standard, integral component of rail inspections. Our specialists use their wealth of experience in combination with quick and simple methods to determine the most suitable action. Any abnormalities they notice will then require further testing.
Eddy current testing
An established method for detecting and evaluating surface defects in the running surface and the running edge down to a depth of 2.7 mm. By fully exploiting the probe’s depth range, we can quantitatively determine the crack length and crack depth of head checks very precisely.
Ultrasonic testing
The most widely used method for detecting internal defects in the rail’s head, web and base. In addition to detecting internal irregularities, our cutting-edge inspection system also detects squats, deep head checks and corrosion in the rail base.
Magnetic particle testing
Magnetic particle testing can detect cracks or bonding flaws in components that can be magnetized, and is used in particular to test the quality of welds.
Magnetic leakage flux testing
This new procedure uses a magnetic field and changes in the flux lines to draw conclusions on the size, shape and position of rail defects. The procedure detects cracks such as head checks or squats down to depths of between 0.4 and 5 mm below the rail surface.