- Approved and used by DB
- High performance
- Long period of operation thanks to system autonomy
- Suitable for high-speed lines
- High planning accuracy
- Equipped according to requirements
- Modular configuration
SF03 W-FFS Rail-Milling Train
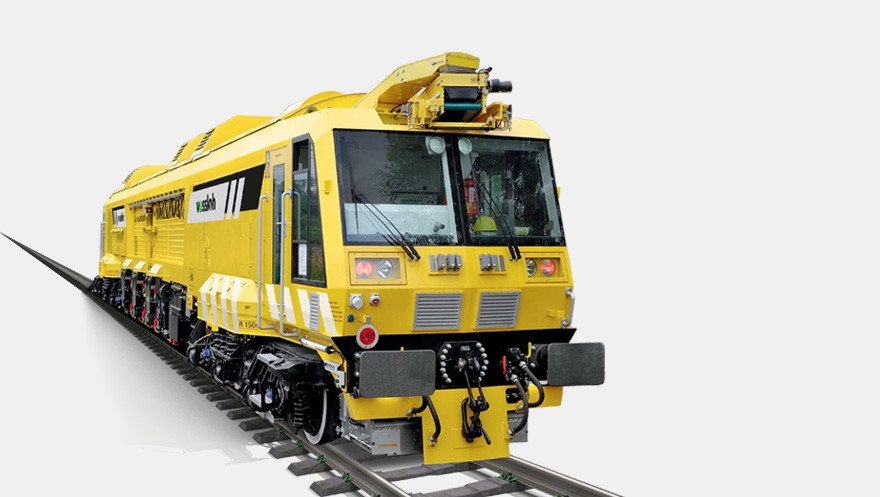
Suitable for high-speed lines
Removes both cross-profile and longitudinal profile rail head defects
Rail profile modification possible
Machining depth on the running surface: 0.3–1.8 mm machining depth
Extraction technology: produces neither sparks nor dust
Suitable for high-speed lines
Removes both cross-profile and longitudinal profile rail head defects
Rail profile modification possible
Machining depth on the running surface: 0.3–1.8 mm machining depth
Extraction technology: produces neither sparks nor dust
Proven. Reliable. Exact.The classical rail-bound milling method
Depending on the rail's condition and the defect depth, this rail-milling train manufactured by Linsinger can machine the rail's entire profile in only a single pass. The integrated grinding technology also fine-grinds the rail, and in so doing further extends the rail's service life. The SF03 W-FFS can operate independently for up to 8 hours and is environmentally-friendly thanks to the minimal dust and sparks produced.
Top-Features
