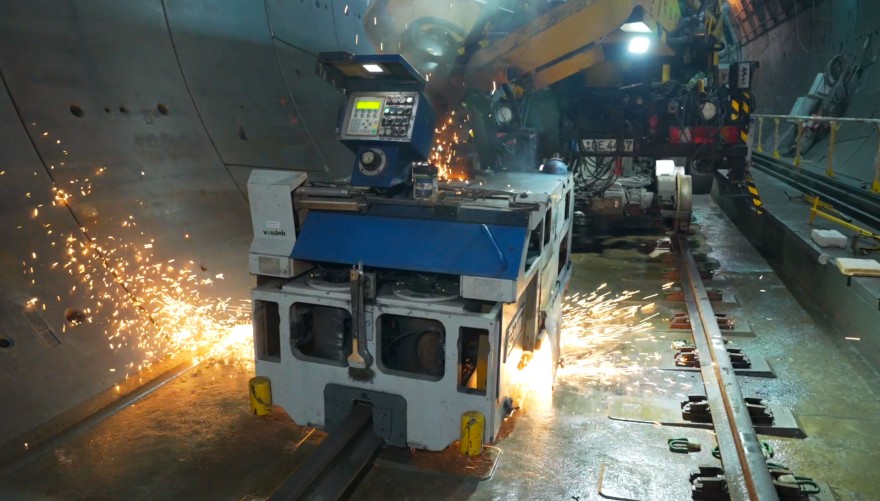
Mobile flash-butt welding – fully automatic process for precision results
Flash-butt welding is a procedure by which electrically conductive workpieces with large cross-sections are heated using electrical energy to the point of melting and then bonded together using high pressure. During the welding process, the contact between the ends of the rails is always only very brief. The high current density that this produces causes the material at these contact points to melt, boil and blow out in a shower of molten particles. This burning away or flashing process also removes any impurities.
We favor the mobile flash-butt welding procedure because of its high-quality results and the speed at which the work progresses. Since the qualitative requirements and standards in the technical codes are identical for both mobile and stationary welding – in this case, for producing long rails – with Vossloh you always get tracks of the highest quality.
How it works
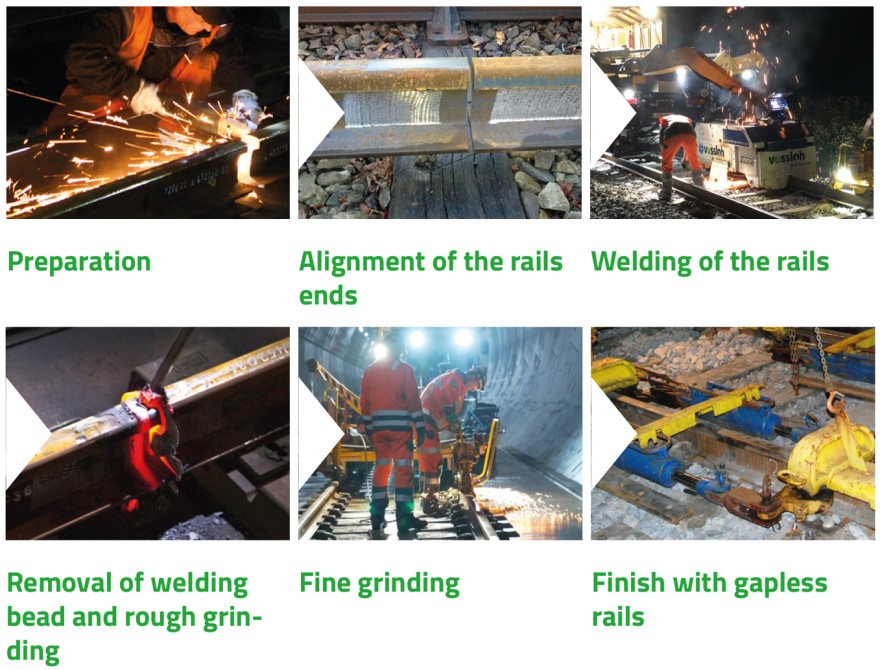
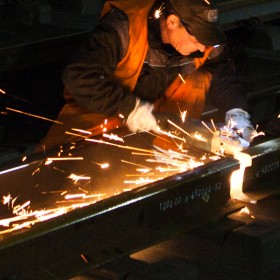
1. Preparation:
creating clean contact surfaces for applying current and in the zone around the rail ends to be welded together.
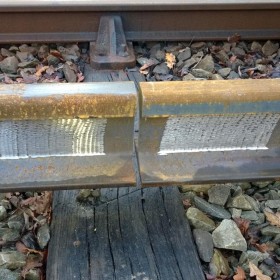
2. Alignment of the rails ends to each other. Loose rails are aligned to the fixed rails (location of the machine) and clamped together. The explosive volatility at the points of contact causes some of the molten metal to spray out, so a forward feed movement is required to maintain contact during the flashing phase.
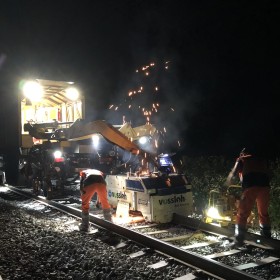
3. Welding of the rails.
a. Electrical voltage is attached to both rail ends.
b. Hydraulic force is used to repeatedly press the moving rail against the fixed rail and retract it again at very short intervals.
c. This creates an electric arc that heats up the rail ends.
d. Once the rail ends reach a temperature of 1 400°C, they are forced together with a force of 600 kN, pushing oxides and impurities into the welding bead.
e. The process is fully automatic and controlled by a dedicated weld processor, monitoring the distance or length of material burned off, the force with which the rails are pressed together, and the current that flows through the rails. Everything is recorded and displayed in a diagram.
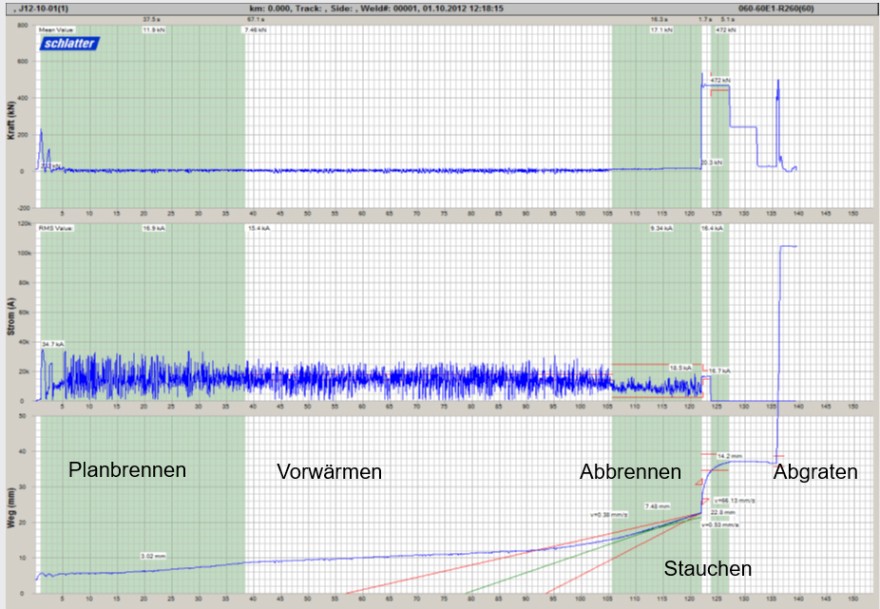

4. Removal of welding bead and rough grinding. While the weld is still warm, the welding bead is removed and the rail is roughly grinded.
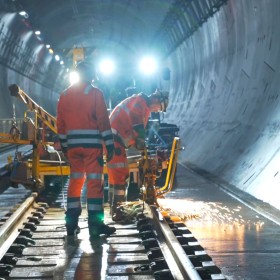
5. Fine grinding. When the rail has cooled down, it is fine grinded.
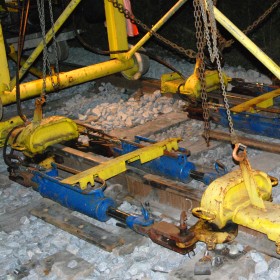
6. Finish with gapless rails. The gaps created at the end of every track section by the positioning of the joints between the sleepers, the mobile welding and the destressing work are closed using made-to-measure rail lengths.
Areas and limits of application
- Our teams have worked on three different continents – on mainline, high-speed, light rail and depot tracks.
- Ambient temperature: between -10°C and 55°C
- Working altitude: up to 3000 meters above sea level
- Smallest radius: 350 m
- Incline/decline: 40 ‰
- Rail profile: Flange rails 36-68 kg/m (S41–R65) – no grooved rails
- Rail length: up to 120 meters without restrictions
- When using "soft" ZW – rest rails on rollers
- Rails longer than 180 meters – rest rails on rollers
- Rest rails between 180 and 300 meters on large rollers - Cannot be used on switches or crossings or as a final weld
Follo Line Tunnel Project 100 meters under the ground at high speed
In the third quarter of 2021, we worked on the Follo Line Project south-east of the Norwegian capital of Oslo. Vossloh is currently the only company approved to carry out flash-butt welding in Norway. The Vossloh team used its welding truck to carry out more than 700 welds in the almost 20-km-long tunnel inside 5 weeks. This was followed by the fine-grinding accurate to a tenth of a millimeter that is specified for high-speed lines. This then completed the work on schedule.
Big campaign on the high-speed lines in Germany
Maximum flexibility, teamwork and full commitment are the order of the day during the ongoing general overhaul of various high-speed lines in Germany. With projects of this scale, the logistical challenges are often that different works are being carried out at the same time on the same section under construction. On the first section of the SFS 1733 line under construction between Hanover and Göttingen around 35 Vossloh employees including our material planning experts handled the coordination of what was required daily. More than 1,500 welds were carried out in a total of 70 shifts on the 90-km-long, dual-track high-speed line and in the tunnels. The flash-butt welding was carried out in combination with the track destressing, or rail neutralization, that was also required. Around 140 welds with a short pre-heating phase were also carried out on switches, level crossings and used as final welds. This procedure is an aluminothermic fusion welding method with a short pre-heating phase. An exothermic process melts the metal, which then flows into the gap between the rail ends encapsulated in a mould. The Vossloh inspection team then carried out the ultrasonic testing required to ensure that the welds were free of any defects. A final acceptance test of the quality of the rail’s longitudinal profile was also carried out on the gauge corner and the running surface because the best possible track geometry ensures that the rails are safe and have a long service life. At speeds of more than 230 km/h, the maximum tolerance that DB accepts on the running surface in the zone 50 cm on either side of the weld is 0.1 mm. Although a good weld is already quite smooth, this level of precision can only be achieved manually by experienced specialists using hand-held grinders.
Better progress on the construction at the Sneltram Project in Utrecht:
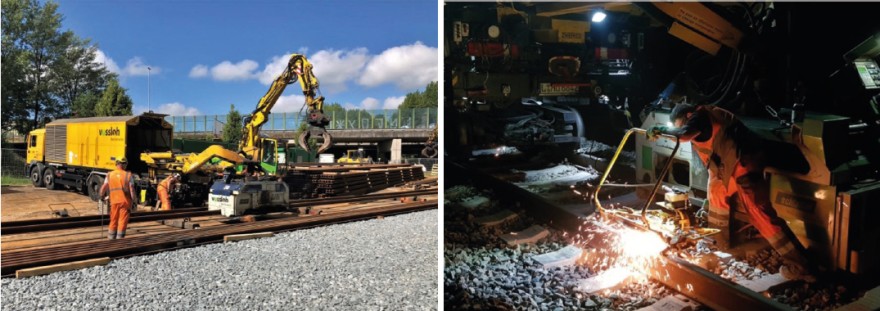
We managed to speed up progress on the construction work on the Sneltram Project in Utrecht by prefabricating long-welded rails near the work site in accordance with the rail plan. This allowed us to:
1. minimize the rail transports
2. reduce the number of field welds required and
3. improve the quality of the welds thanks to flash-butt welding.
The 30-meter-long flange rails were fed into the mobile welding plant using excavators, and once they had been welded into 120-meter lengths they were taken straight to the worksite on flatcars. We carried out a total of more than 850 welds including almost 60 welds in less than nine hours, which even for us was a real project highlight.
Doha Metro: working in a confined space
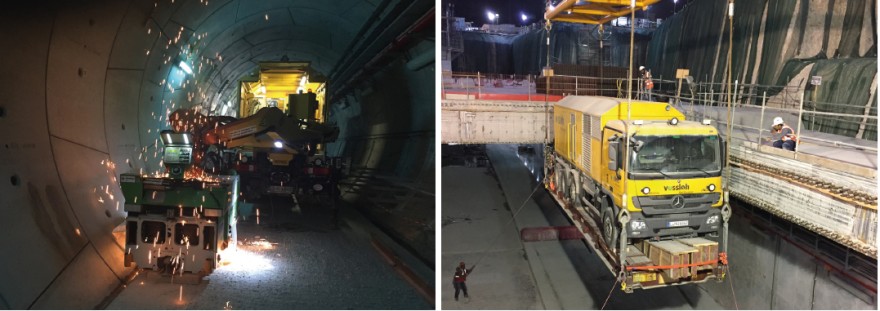
One of our very special projects was the new metro system in Doha. A 76-km metro system comprising three lines and 37 stations that connects the airport with the city center and the stadiums was built in preparation for the 2022 Football World Cup in Qatar. 18-meter-long rails were shipped in from Japan, brought into the tunnel using a crane, and prefabricated into 108-meter-long rails using a kind of semi-stationary welding installation. These were then welded together in the tunnel to create continuous welded track. In 10 months, we carried out around 4,000 welds in a very confined space in temperatures in some cases of almost 40°C and extremely high humidity in a matter of months – despite nightshifts. We were helped by the fact that there was very little fluctuation in the ambient temperature, so we didn’t need to destress the track using hydraulic pulling equipment before welding the rails together. The rails underwent precise elongation in the 120-meter zone heading in and out of the tunnel, so that each rail of the track can absorb the compressive forces at high temperatures and absorb the tensile forces acting on it at correspondingly low temperatures. We also produced long welded rails for connecting the numerous switches and crossings while the wagon depot buildings and maintenance halls are being erected.
Download
Take advantage of the benefits of professional mobile flash-butt welding
- Higher quality and stronger weld
- Process is stable thanks to processor control
- No foreign materials are employed (electrode, mould sand, thermite material) so there are also no accretions, slag or welding residues
- Highly productive in a short period (up to 8 welds an hour)
We'd be glad to help you with your project implementation.