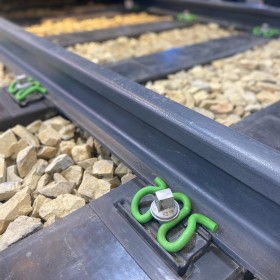
- The objective: an ecological compound sleeper that combines the positive features of wooden and existing plastic sleepers
- Increased safety thanks to the incorporation of reinforcement (as with concrete sleepers)
- Initial market situation: planned creosote ban for wooden sleepers in Europe – unfortunately postponed for 2 years
- Further motivations for the development: “enabling green mobility”
- Confidence in own competencies & abilities: interaction during wheel-rail contact & Technology Centre in Werdohl for all test scenarios